Porosity in aluminum alloy die casting production
What is the cause of porosity?
Porosity in aluminum alloy die casting production
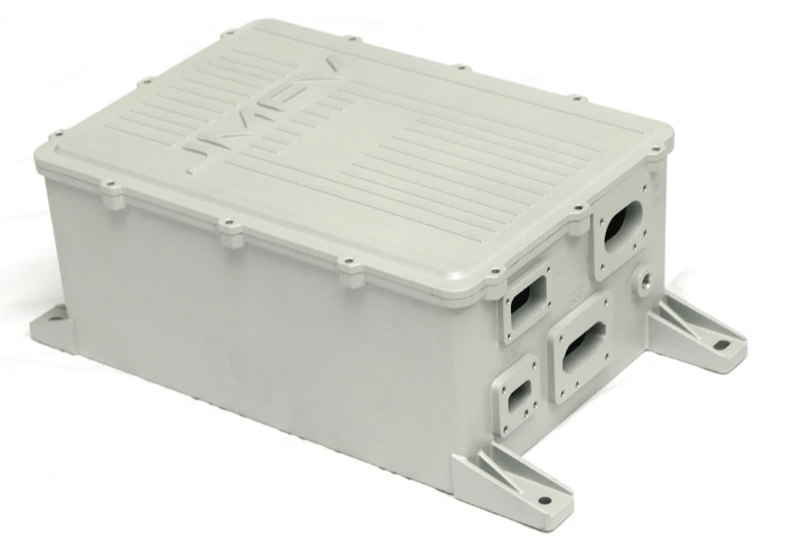
In the production of aluminum alloy die casting, people often generally call the holes of products as pores, so what are these pores caused by? Let's make a brief analysis:
1、 Pores due to poor degassing quality in refining
In aluminum alloy die casting production, the pouring temperature of molten aluminum is usually 610 º C to 660 º C. at this temperature, a large amount of gas (mainly hydrogen) is dissolved in the aluminum alloy. The solubility of hydrogen aluminum alloy is closely related to the temperature of aluminum alloy. It is about 0.69cmj/100g in liquid aluminum at about 660 º C and only 0.036cm in solid aluminum alloy at about 660 º C ³/ 100g. At this time, the hydrogen content in liquid aluminum is about 19-20 times that in solid state. Therefore, when aluminum alloy solidifies, a large amount of hydrogen will be separated out and exist in aluminum die castings in the form of bubbles.
The purpose of refining and degassing in the process of aluminum alloy melting is to reduce the gas content in aluminum water and prevent a large amount of gas from forming pores on the surface of aluminum alloy solidification. If the content of gas is reduced in liquid aluminum, the amount of gas precipitated during solidification will be reduced, so the bubbles will be reduced and significantly reduced. Therefore, the refining of aluminum alloy is a very important process means. With good refining quality, there must be fewer pores, poor refining quality and more pores. The measure to ensure the refining quality is to use a good refining agent. A good refining agent can react at about 660 º C to produce bubbles. The bubbles are not too violent, but evenly and continuously produce bubbles. Through physical adsorption, these bubbles are in full contact with the liquid aluminum, and the longer the better. Generally, it takes 6-8 minutes to bubble.
When the aluminum alloy is cooled to 300 º C, the solubility of hydrogen in the aluminum alloy is only 0.001 cm ³/ Below 100g, it is only 1 / 700 of that in liquid state. The pores produced by hydrogen precipitation after solidification are dispersed and small pinholes, which do not affect the gas and processing surface, and are basically invisible to the naked eye.
During the solidification of liquid aluminum, the bubbles produced by hydrogen precipitation are relatively large, mostly in the heart of the final solidification of liquid aluminum. Although they are also dispersed, these bubbles often lead to leakage. Serious often leads to workpiece scrapping.
2、 Air holes due to poor exhaust
In aluminum alloy die casting, due to the poor exhaust channel of the die and the poor exhaust design structure of the die, the gas in the die cavity cannot be completely discharged smoothly during die casting, resulting in pores in some fixed parts of the product. The pores formed by the gas in the mold cavity are large and small, and the inner wall of the pores is the oxidation color of aluminum and air. Unlike the pores generated by hydrogen precipitation, the inner wall of the hydrogen precipitation pores is not as smooth as the air holes, and there is no oxidation color, but a gray and bright inner wall.
For the pores caused by poor exhaust, the exhaust channel of the die should be improved, and the residual aluminum skin on the exhaust channel of the die can be cleaned in time.
3、 Air hole caused by improper die casting parameters
In die-casting production, the die-casting parameters are improperly selected, and the filling speed of aluminum water die-casting is too fast, so that the gas in the cavity can not be completely extruded out of the cavity in time and stably, but is drawn into the aluminum liquid by the liquid flow of aluminum liquid. Due to the rapid cooling of the aluminum alloy surface, it is wrapped in the solidified aluminum alloy shell and can not be discharged, forming large pores. This kind of air hole is often below the surface of the workpiece. The aluminum water inlet is less than the final confluence, in pear shape or oval shape, and more and larger at the final solidification.
For such pores, the filling speed should be adjusted to make the aluminum alloy liquid flow advance smoothly without high-speed air entrainment.
4、 Porosity and shrinkage porosity due to shrinkage of aluminum alloy
Like other materials, aluminum alloy shrinks during solidification. The higher the pouring temperature of aluminum alloy, the greater the shrinkage. A single pore caused by volume shrinkage exists in the last solidification part of the alloy. It is irregular in shape and reticular in severe cases. In the product, it exists simultaneously with the pores precipitated by hydrogen during solidification, there are shrinkage pores around the hydrogen precipitation pores or roll pores, and there are filamentous or reticular pores extending to the outside around the bubbles.
For this kind of air hole, the pouring temperature should be solved. When the die-casting process conditions allow, the pouring temperature of molten aluminum during die-casting should be reduced as much as possible. This can reduce the volume shrinkage of castings, reduce shrinkage pores and shrinkage porosity.
If such pores often appear at the feeding part, it can be considered to add core pulling or cold iron to change the final solidification part to solve the problems of leakage and feeding defects.
5、 Pores caused by excessive product wall thickness
There is often a problem of too large wall thickness difference in the shape of the product, and the shape of the product can not be changed. In the center of the wall thickness is the place where the molten aluminum finally solidifies, and it is also the place where pores are most likely to occur. The pores at the wall thickness are a mixture of precipitation pores and shrinkage pores, which can not be prevented by general measures.
When designing the shape of the product, we should consider reducing the problem of uneven wall thickness or excessive thickness, and adopt hollow structure. In the mold design, we should consider adding core pulling or cold iron, or water cooling, or increasing the cooling speed of the mold.
In die casting production, pay attention to the undercooling of this part and appropriately reduce the pouring temperature.